Pendant la période COVID-19, Lenovo a construit une nouvelle usine en Hongrie pour que ses stations de travail et ses serveurs portent le label « Fabriqué in Europe ». Mais ce n’est pas la raison principale : le site doit répondre à des objectifs écologiques concrets et garantir une chaîne d’approvisionnement solide.
L’usine d’ordinateurs de bureau et de serveurs flambant neuve de Lenovo en Hongrie compte 5 072 panneaux solaires sur son toit, soit une production d’environ 3 MW. Mais aujourd’hui, le rendement est plus proche de zéro : le ciel de Budapest et de ses alentours est caché par de gros nuages, et une pluie incessante s’en échappe. Nous ne sommes pas sûrs s’il faut monter sur le toit du site pour voir les panneaux.
Une ambition sans bornes
Le temps déplorable n’empêche pas Szabolcs Zolyomi, responsable du site de la chaîne d’approvisionnement, et Stefan Larsen, responsable des services mondiaux de développement durable, d’activer le site en appuyant sur un gros bouton. Un bon symbole. « Pour arrêter l’usine et la réactiver, il faudrait la fermer, et on ne le fera pas », s’amuse Zolyomi. Il n’est pas gêné par le temps : « Des panneaux solaires sous la pluie, voilà qui montre comment nous sommes invincibles. »
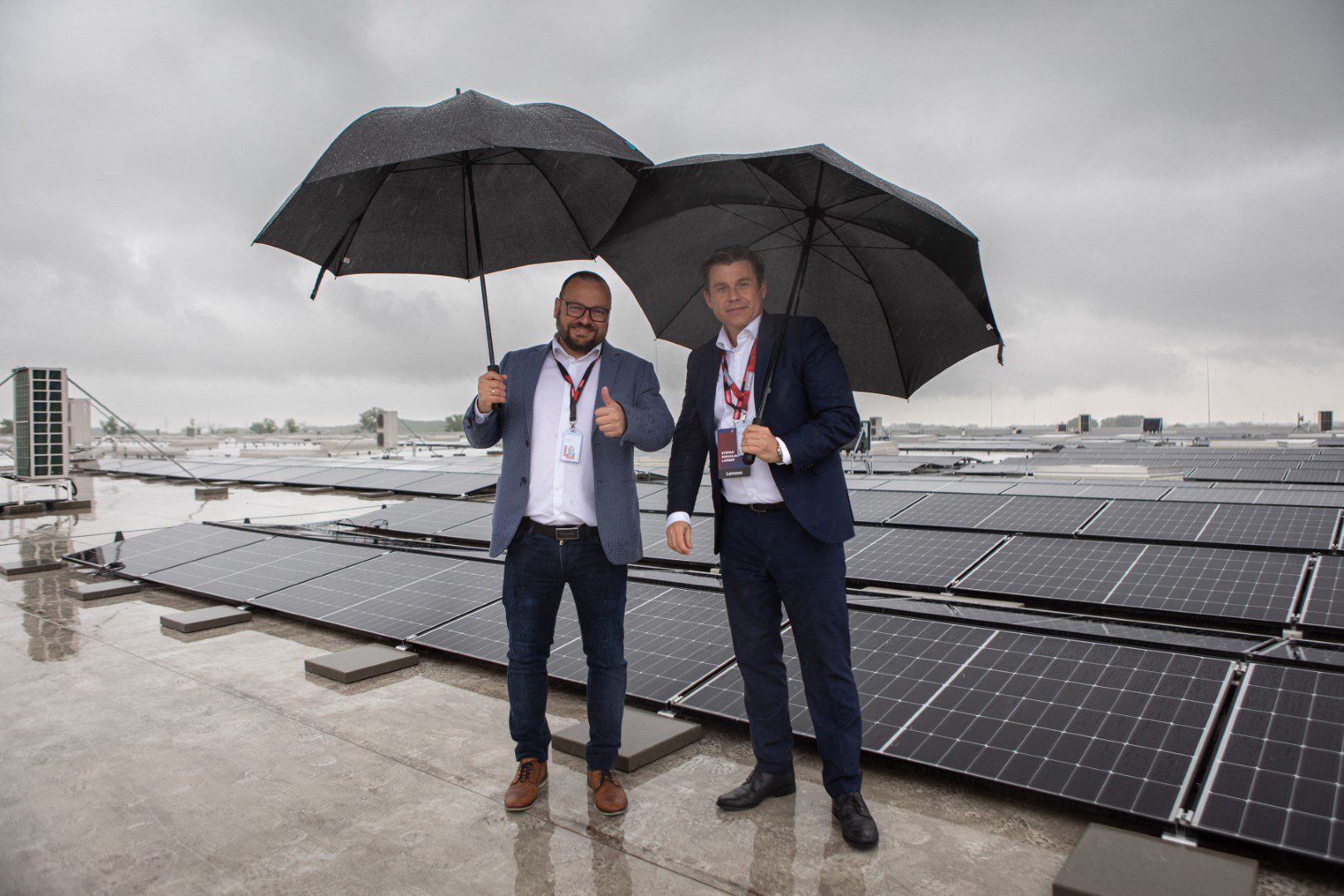
La presse est invitée à l’usine hongroise pour célébrer l’activation des panneaux solaires, mais en réalité, Lenovo souhaite attirer l’attention sur l’importance plus large de la durabilité, fondée sur l’initiative objectifs fondés sur la science. Un autre thème clé est l’impact positif du site sur la stabilité de la chaîne d’approvisionnement européenne et mondiale.
Des panneaux solaires sous la pluie, voilà qui montre comment nous sommes invincibles.
Szabolcs Zolyomi, chef de site de la chaîne d’approvisionnement Lenovo Budapest
« En 2020, cet endroit était encore un champ de blé », explique Zolyomi. « Malgré les restrictions liées à COVID-19, nous avons mis dix mois pour construire le bâtiment. Encore sept mois plus tard, les lignes de production y étaient installées, ainsi que le centre d’innovation IA & HPC. Aujourd’hui, nous essayons d’augmenter la production en augmentant la densité. »
Plusieurs options
COVID-19 a révélé les limites de la chaîne d’approvisionnement mondiale. L’usine de Budapest, dont la construction était planifiée par Lenovo depuis 2016, devrait la rendre plus solide. Depuis son usine, le spécialiste de l’informatique fournit des serveurs, du matériel HPC et des ordinateurs de bureau à la région EMOA, mais toute usine est équipée pour des commandes partout dans le monde.
En revanche, les composants que les ouvriers utilisent pour assembler le matériel en deux équipes proviennent encore principalement d’Extrême-Orient.
« Notre but est d’avoir au moins deux sources d’approvisionnement pour toutes les pièces », explique Brian Jaeger, directeur des services de la chaîne d’approvisionnement. « Pour nos propres produits, c’est chose faite. Pour les pièces fournies, nous parlons de centaines de milliers de composants. Quatre-vingt-quinze pour cent de l’approvisionnement de ces pièces est désormais également diversifié. »
Assemblage sans bruit
Une fois protégés de la pluie, à l’intérieur de l’usine, nous sommes surpris par le silence relatif qui règne. Des serveurs et des ordinateurs de bureau bourdonnent dans les bancs de test et des travailleurs travaillent sur diverses lignes de production, mais dans l’ensemble, le vaste hall de l’usine est plutôt calme. Les logos Lenovo sont bien visibles, ainsi que des photos inspirantes de centres de données tels que Mare Nostrum à Barcelone, pour lequel ce site fournit les nœuds et les racks.
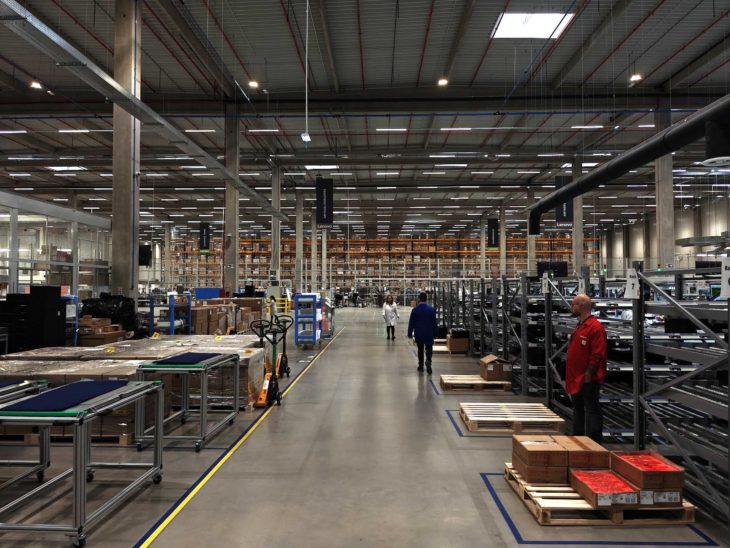
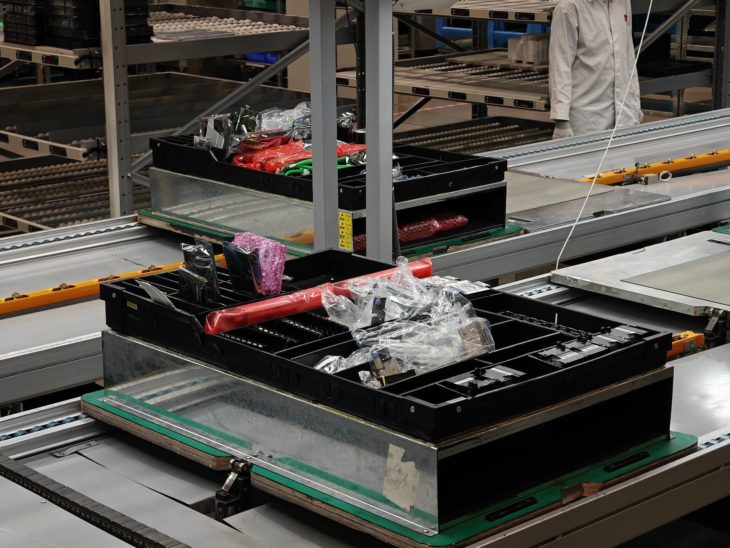
« Pour les grosses commandes, l’assemblage se fait sur la chaîne de montage », explique Zolyomi. « Chaque personne sur la bande exécute une opération et l’ensemble de la chaîne de production est optimisé pour éviter les goulots d’étranglement. Pour les commandes spéciales, les magasiniers assemblent d’abord tous les composants dans une boîte à sushis (une grande boîte avec des compartiments pour les différents composants, ndlr.), puis un spécialiste prépare l’ensemble du serveur sur mesure. »
Sur la chaîne de montage, on voit les employés exécuter systématiquement une tâche spécifique. Ils installent des ventilateurs, des disques durs ou des GPU, après quoi le serveur en attente passe à la station suivante. Pour les actions répétitives, comme le vissage de certains composants, des robots aident les travailleurs.
Pour les commandes spéciales, on procède différemment. D’autres personnes remplissent activement des bacs avec des composants provenant de l’immense entrepôt, qui partent ensuite par un autre tapis vers les assembleurs spécialisés. Comme sur des roulette, et tout le monde connaît son rôle. Les jaquettes colorées indiquent ces rôles : blanc pour les ouvriers des tapis, bleu clair pour le contrôle de la qualité, jaune pour les instructeurs et rouge pour les superviseurs. Nous avons porté une jaquette vert clair, défiant ainsi la mode, indiquant que nous étions des visiteurs. « Cela évite d’être soudainement mis au travail par un instructeur », s’amuse Zolyomi.
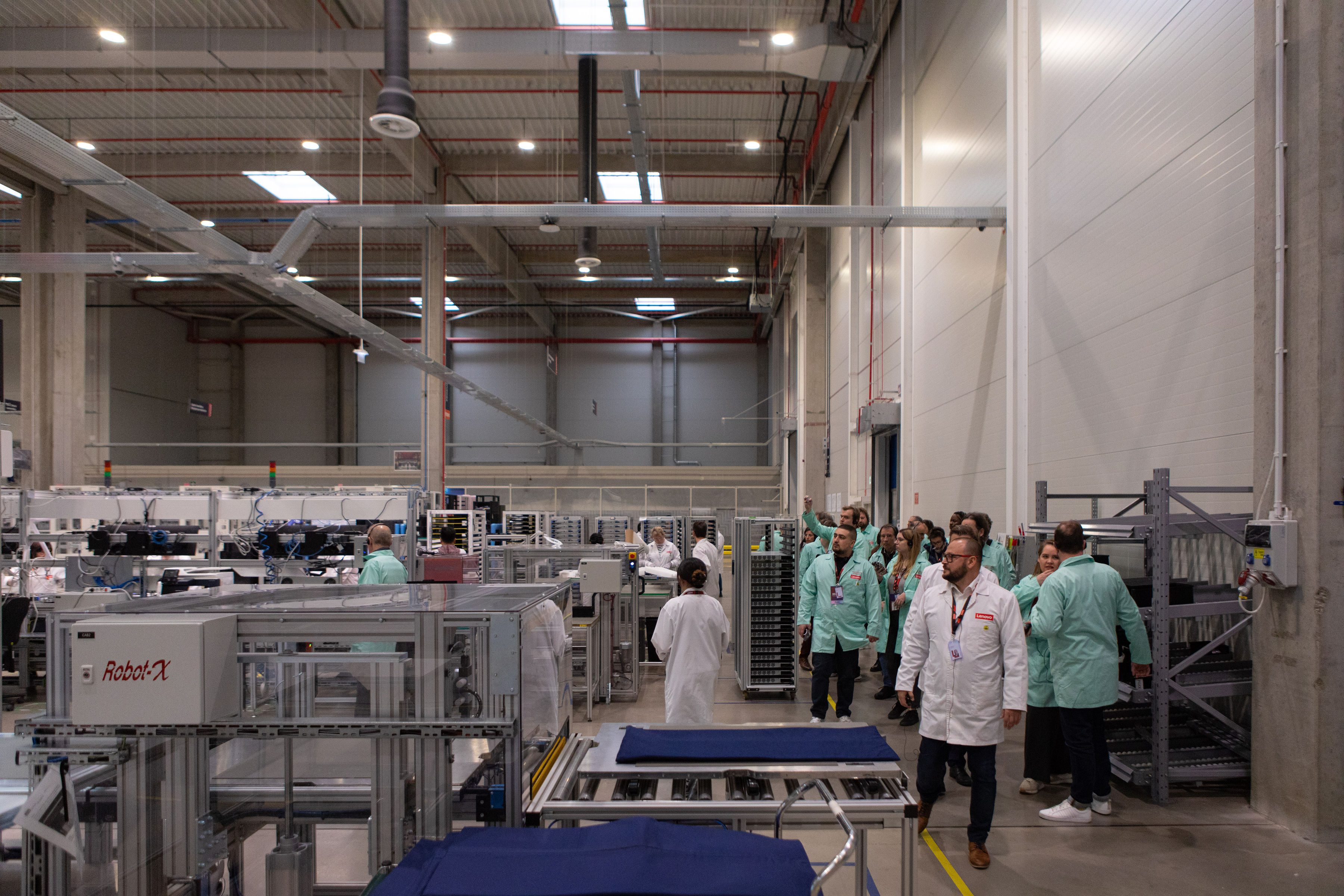
Conducteur piloté par ordinateur
Toutes les activités de l’usine sont entièrement numérisées. Zolyomi : « Tous les composants sont scannés avant d’être installés. La numérisation d’une pièce défaillante génère un code d’erreur. L’inventaire des produits diminue quand les pièces sont scannées. Comme chaque pièce a un code unique, nous pouvons retracer les problèmes par la suite. »
Tous les employés travaillent de concert avec le cerveau numérique de l’usine, qui utilise des outils d’analyse pour déterminer quelles commandes arrivent à quel moment. » Ces algorithmes sont exécutés dans un centre de données situé dans l’usine « , explique Jaeger, mais nous n’avons pas eu accès à ce cerveau numérique au cours de notre visite.
Chaque poste de travail est équipé d’un écran et d’un lecteur de codes-barres : tous les employés peuvent ainsi voir à tout moment ce qu’ils ont à faire. Dans les zones centrales de l’usine, des écrans permettent de suivre l’état d’avancement des travaux à l’aide de graphiques et de codes de couleur.
« L’usine fonctionnerait sans doute même sans cette numérisation complète », pense Zolyomi. Mais c’est comme si l’on conduisait une voiture sur l’autoroute sans compteur de vitesse, sans jauge d’essence et sans rétroviseurs. Grâce à tous ces outils, on sait encore mieux faire.
Tester, refroidir et chauffer
Au centre du hall d’usine, se trouve un bâtiment plus petit. Le calme qui règne dans les autres lieux n’y existe pas. Des centaines de serveurs dans des dizaines de racks hurlent. C’est ici que Lenovo injecte le logiciel et que le matériel est testé.
Certains racks sont refroidis de manière traditionnelle, mais on voit aussi des serveurs Neptune refroidis à l’eau. De plus, dans le coin le plus éloigné se trouvent des serveurs HPC qui font partie du Centre d’innovation, auquel les experts peuvent accéder via une connexion VPN. La chaleur générée par ces systèmes refroidis à l’eau passe par les radiateurs des salles de réunion du site.
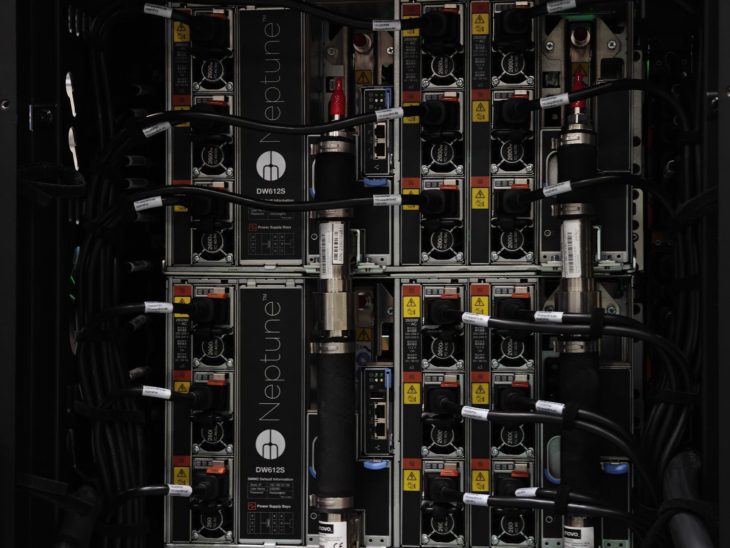
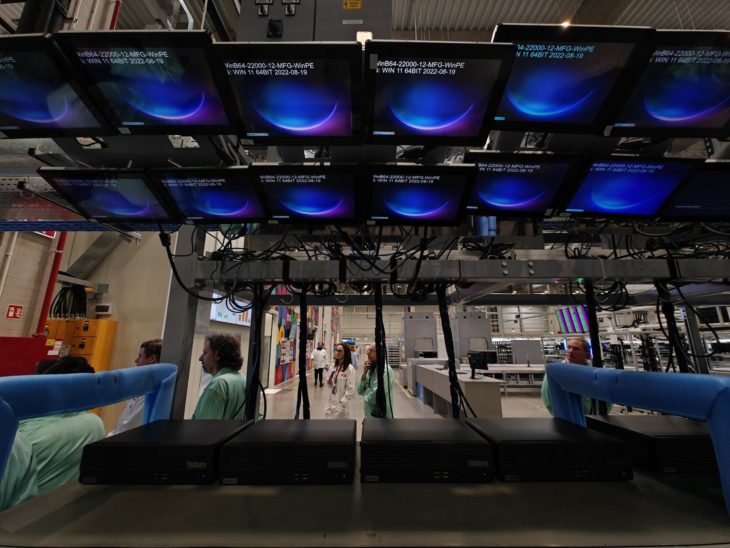
« Tout le bâtiment a été conçu en gardant le souci de la durabilité », explique Zolyomi lors d’une présentation dans l’une de ces salles de réunion. « Nous n’utilisons pas seulement la chaleur perdue des serveurs, mais nous refroidissons aussi avec de l’air extérieur chaque fois que c’est possible. Le bâtiment est bien isolé et contrôlé par un système intelligent qui détecte la température et l’humidité, et peut s’allumer et s’éteindre tout seul. »
Culture ESG
Lenovo présente toutes les données en temps réel sur la consommation d’eau et d’électricité de l’usine à l’entrée du hall de production, afin que les employés puissent les contrôler. « Nous créons ainsi une culture de la durabilité parmi nos employés », dit Zolyomi.
À l’arrière de l’usine, les serveurs assemblés et testés sont emballés de la manière la plus durable possible. Là encore, des personnes scannent les produits, puis une ventouse les prend afin que les travailleurs puissent les guider vers la boîte sans risquer de se blesser le dos.
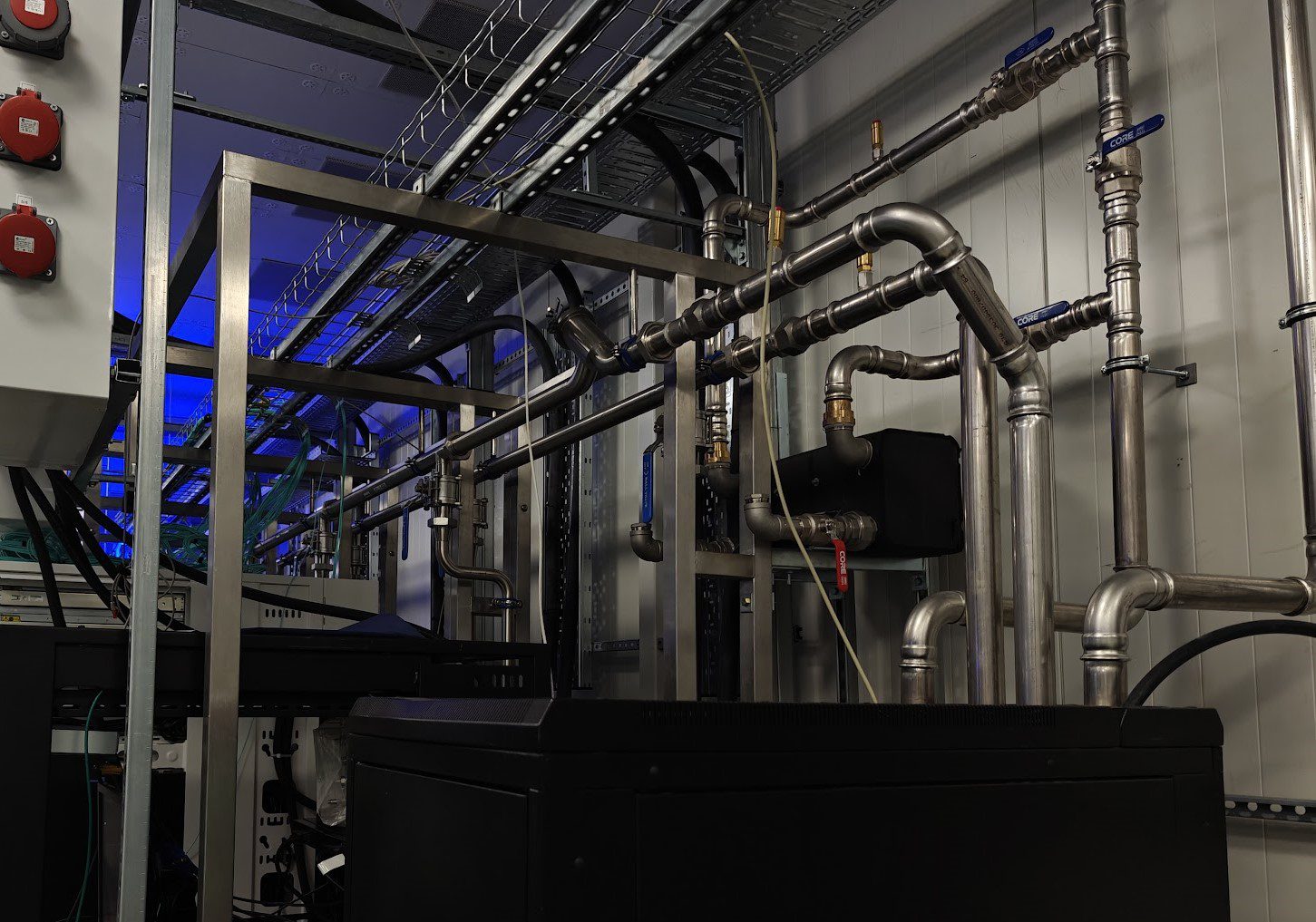
Si possible, Lenovo met plusieurs appareils dans le même emballage. Les racks remplis de nœuds sont remis dans leur emballage d’origine et seule l’étiquette est changée, si le client final est d’accord. Quant aux nouveaux matériaux d’emballage, ils proviennent tous de fournisseurs locaux. Toutes les boîtes de serveurs et de stations de travail finis portent fièrement la mention « Fabriqué en Europe ».
« Nous expédions presque tous les systèmes finis par camion », sait Jaeger. « Seulement dans un cas exceptionnel, si la livraison doit se faire rapidement, nous optons pour le transport par avion », précise-t-il. Cela fait partie de la stratégie de Lenovo en matière de développement durable.
Ancrage européen
En sortant, nous voyons les ouvriers continuer à travailler. « On a 15 nationalités ici », ajoute fièrement Zolyomi. « Cette usine a créé plus de 1 000 emplois dans la région et la main-d’œuvre a encore augmenté de 20 % ces dernières années. »Même si Lenovo est une entreprise chinoise aux racines américaines, l’ambition d’un ancrage européen fort est visible.
À la sortie, la pluie ne cesse de tomber. Les jours ensoleillés, les panneaux solaires installés sur le toit produisent plusieurs fois l’énergie dont le site a besoin pour fonctionner. Lenovo l’injecte ensuite dans le réseau hongrois, car le site ne possède pas de grandes batteries. Personne n’ose vraiment estimer le nombre de kilowatts que les panneaux solaires produisent aujourd’hui.